TARBO MIX > Functions
Functions
“TARBO MIX” is an epoch-making continuous high-pressure foaming mixer that offers a wide variety of usages and applications that conventional continuous mixers cannot offer.
Thanks to the special structure that positively equalizes the pressures inside the mixing unit, as well as segmentation of the cooling (temperature maintenance) system, the manufacturing of products in a wider range and with a higher quality has been made possible. In addition, combination with a pre-process machine and/or a post-process machine has led to automatization of manufacturing lines in various fields, which has allowed the mixer to become widely used in confectionary factories, the fish/food processing field, and the chemical field.
❶Easy operation
Control panel on the main machine
It is possible to easily change the production amount and specific gravity, as well as set and adjust the emulsification condition of product and viscosity. Due to the real-time indication of product specific gravity and product temperature, the production line can be easily controlled. The capability to register 20 types of production data makes it possible to conduct automatic operation.
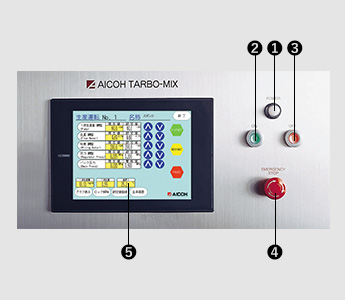
❶Power lamp
❷Main switch ON
❸Main switch OFF
❹Emergency stop button
❺LCD display
Operation screen
10.4-inch TFT color LCD panel that emphasizes ease of use and view at production sites. Items to be constantly used are displayed clearly.
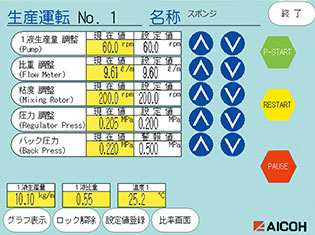
Program screen
When multiple setting values have been input in advance, only changing “Production amount” changes other data in an interlocked manner (automatic setting software).
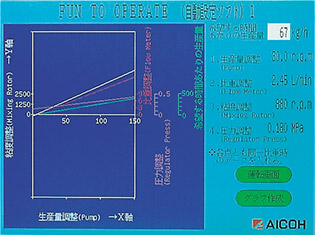
❷Quantitative material feed
Production amount adjustment pump made of stainless steel
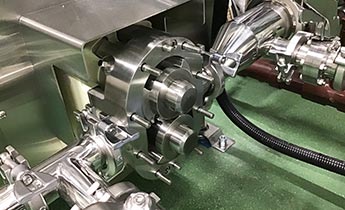
This pump feeds a predetermined amount of the material in the holding tank to the mixing head. As the rotor and the stator do not make contact with each other, it is possible to use high-temperature water. The pump has a good cleaning performance and is also suitable for CIP cleaning.
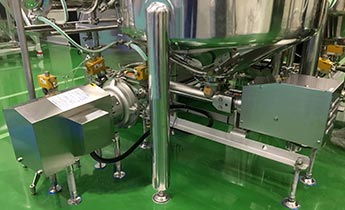
This pump is employed for the quantitative feeding of highly-viscous material, a two materials mixture control system, and other uses. It is resistant to pressure change and allows for the fine adjustment of feed amount, and therefore is suitable for the production of products with relatively light specific gravity.
Pre-mix storage tank Holding tank
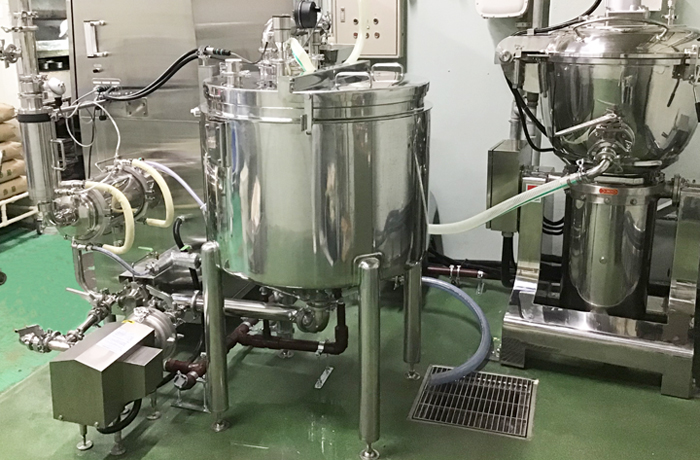
The holding tank, into which materials are charged, can conduct jacket cooling/heating in accordance with the usage. It is also possible to install a level sensor, a temperature sensor, CIP cleaning piping, a shower ball, and others for the purpose of material feed control.
❸Determination of specific gravity / mixing in of air
Compressor / mass flow controller
A mass flow controller, which supplies air (such as nitrogen gas) to be charged into a material at a stable flow rate in accordance with the setting value, is employed. Thus, specific gravity is accurately adjusted. As this is a mass flow meter, the flow rate maintains the set air amount even when the pressure is changed.
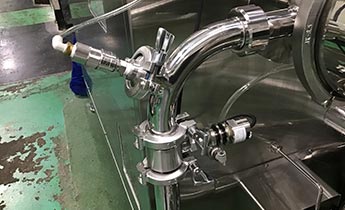

Air injection port
An air injection port is installed at a curved piping section to minimize the accumulation of material and air. Through the employment of a high-performance mass flow rate meter, the port sensitively responds to the change of flow rate. The port also prompts the inflow of cleaning liquid during CIP cleaning, making complete cleaning possible.
❹Adjustment of emulsification condition and viscosity
Mixing head
By conducting high-precision cutting in our factory to decrease the clearance between the stirring pin of the rotor and that of the stator, operation can be performed at a lower rotation speed and a lower pressure than in conventional machines. It is possible to suppress temperature rise and produce high-quality products. The material sent from the pump to the mixing head is transferred to the tip while being stirred, and the air and material are segmented and mixed with each other. By controlling the temperature and internal pressure, it is possible to produce products with a uniform and fine texture.
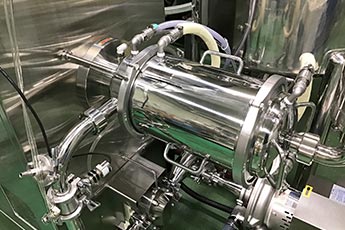
Mixing head Drum type
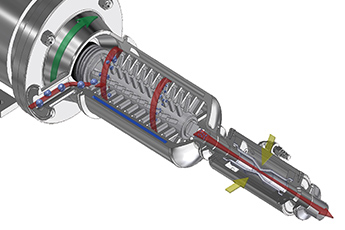
3D image of internal structure of the mixing head
❺Pressure adjustment
Regulator
At the tip of the mixing head is a regulator that adjusts the discharge pressure. Air is fed to the regulator, the product discharge port is narrowed and the material in the mixing head is kept at a constant pressure. Maintaining the set pressure makes it possible to continue stable production.
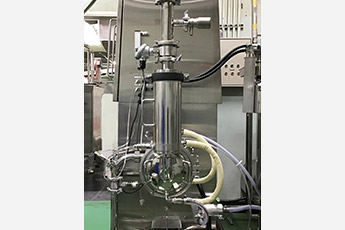
Connection to Drum type
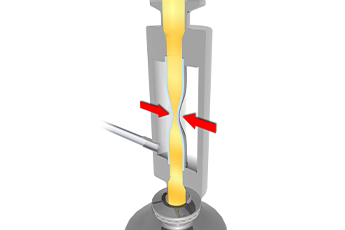
3D image of internal structure of the regulator
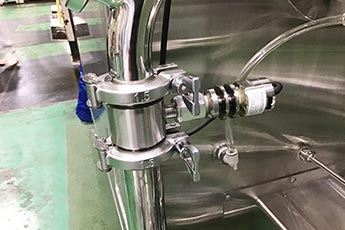
Pressure control
❻Material temperature control
Chiller unit
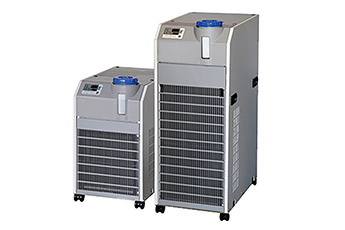
Chiller unit Hot/cold water circulation device (option)
The holding tank, the rotor and stator cooling (heat insulation) unit, as well as units up to the shaft sealing unit that are located between the pump and the mixing head, are equipped with respective circulation systems. The chiller unit reliably conducts temperature control of those circulation systems.
Jacket structure
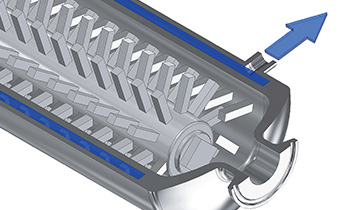
Temperature control is conducted by circulating cold and hot water through the mixing head of a jacket structure.The chiller unit main body is equipped with a tank that circulates hot/cold water in the tank, thus eliminating the need for a water supply.